动力电池是电动汽车关键技术。动力电池单体如何组合成模组?模组如何组合成PACK?目前普遍采用方法是焊接工艺。特斯拉电动汽车的PACK采用的就是激光焊工艺。大家对特斯拉电动汽车采用18650电池,认为并没有什么先进地方,但是对特斯拉的PACK采用的激光焊工艺水平比较高,纷纷点赞。
中国电动汽车动力模组、PACK成组也可以采用激光焊工艺,但是投入大高,质量把控中国目前做不到,普遍认为如果跟特斯拉学,风险极高。下面介绍工艺相对简单、投入不大、质量把控高、可靠性有保障的动力电池模组、PACK纯机械组装技术及实例,分享给同行。
一、电池模组、PACK焊接难点与不足
新能源汽车的发展对动力电池外观、电池容量、电池耐久性等都在不断提出新的要求,激光焊接自然是电池厂商首选生产设备之一。实践证明,其主要的接难点与不足如下:
①如果采用是侧焊工艺,焊接后可能会导致凸起,对后续工艺的装配会有些影响。因此侧焊工艺对激光器的稳定性、材料的洁净度和顶盖与壳体的配合间隙有较高的要求。
②如果采用顶焊工艺,对前道工序入壳及定位要求很高,对设备的自动化要求高。
③表面凸起、气孔、内部气泡是激光焊接的致命伤。目前基本上都铝壳电池,会面临焊痕表面凸起、气孔、炸火、内部气泡问题等。
④动力电池在焊接时是带电作业。无论采用什么焊接工艺,对锂电池而言,都会有不同程度的破坏作用,。
⑤动力电池单体生产过程中一致性控制要求极高,最后还要进行一致性筛选,如需单体电池再进入模组焊接。模组对焊接工艺的一致性要求更高,如果模组的一致性不能保障,前面单体一致性保障措施,没有一点意义。
⑥采用焊接工艺,后续电池梯度利用困难重重。可以说,如果后续的梯次利用,又用焊接工艺,模组的一致性已经没有办法保障了。
焊接工艺实例效果,(见图1)
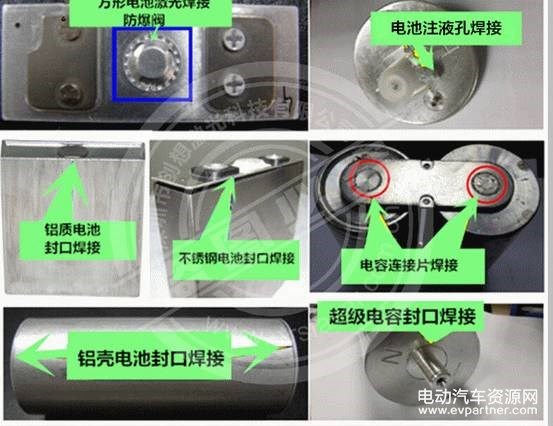
图1 铝壳电池焊接工艺及效果
二、动力电池模组、PACK纯机械组装基本原理
其基本原理:大家比较熟悉的手电筒。1号电池即单体,2节(3节)电池负极接正极,用一个铝壳圆筒将节电池包裹起来,使其固定作业。对负载而言,一个正极、一个负极,两头用帽子拧紧即可。
动力电池模组原理与电筒是一样的,但在工程设计上有本质上的区别。模组每一个单体也是用圆筒座固定起来,即M个圆筒座将M个单体并联起来。在正极(负极)端用金属汇流排,将M个正极(负极)并起来即可。(见图2)
![]() |
![]() |
图2 动力电池模组纯机械组装效果图 |
模组与模组的串联,再用导流板串联即可。
三、模组、PACK纯机械组装技术特点
①结构可靠:抗震动 抗疲劳;
②工艺可控:无过焊、虚焊,确保电芯100%无损伤;
③成本低廉:PACK产线自动化成本低,包括生产设备、生产损耗;
④易分拆:电池组易于维护、维修,低成本,电芯可梯次利用性好。
四、与焊接工艺比较比较分析
① 电芯无损伤,尤其是自放电方面;
②可全工段检测,模块质量可控;
③无发生焊点脱开,抗震动性能优 ;
④BOM成本低于正负极焊接工艺;
⑤投入低,设备自动化程度高;
⑥便于维护成本,电芯可梯次使用;
⑦模块内阻略低于正负极焊接工艺,远于铝丝超声焊。
五、动力电池模组、PACK纯机械组装全自动化产线实例
①适用于18650、21700、26650圆柱形电池;
②动力电池模组纯机械组装线(见图3);
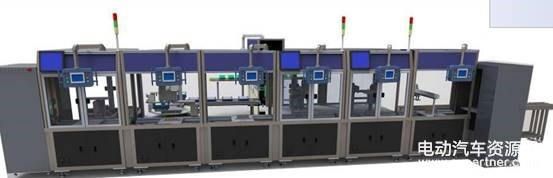
图3 动力电池模组纯机械组装线
③组装线设备清单
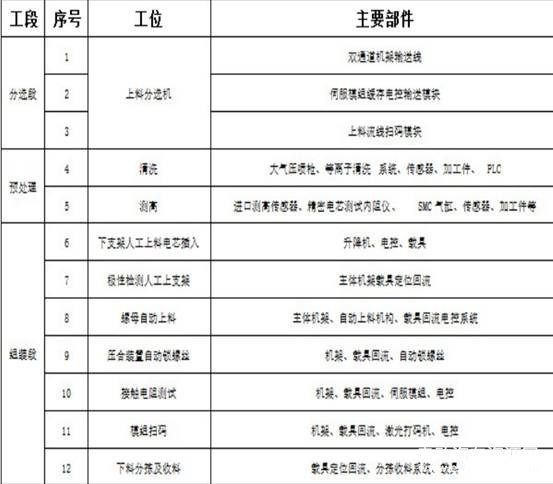
④实车250天、大于500次充放循环的电芯状态
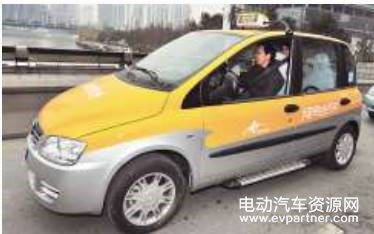
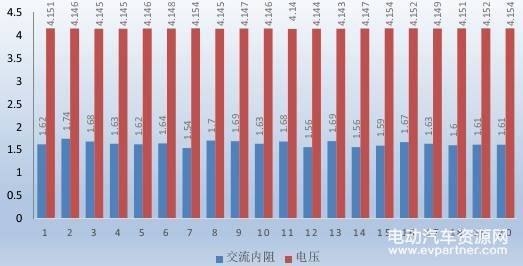
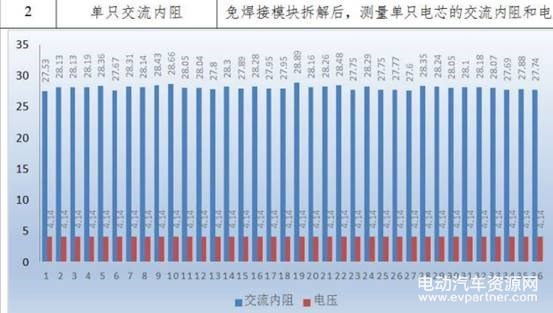
六、拓展应用
动力电池基本分为圆柱形、方形、软包装三大类。目前已经成功实现圆柱形电池模组、PACK纯机械组装。目前有关动力电池几何尺寸的国家标准已经发布。同理,方形、软包也是可以推广应用动力电池模组、PACK纯机械组装技术。这一技术的推广应用,其意义是不言而喻的。